Methods and means to improve the heat resistance of polyurethane materials
浏览量:2380时间:[2020-08-26]
As the main auxiliary agent for polyurethane foaming, color paste is widely used in various polyurethane materials. As a professional polyurethane color paste manufacturer in East China, our factory has the characteristics of high color concentration, good fluidity, large amount of addition does not affect foaming, bright color, and strong weather resistance...
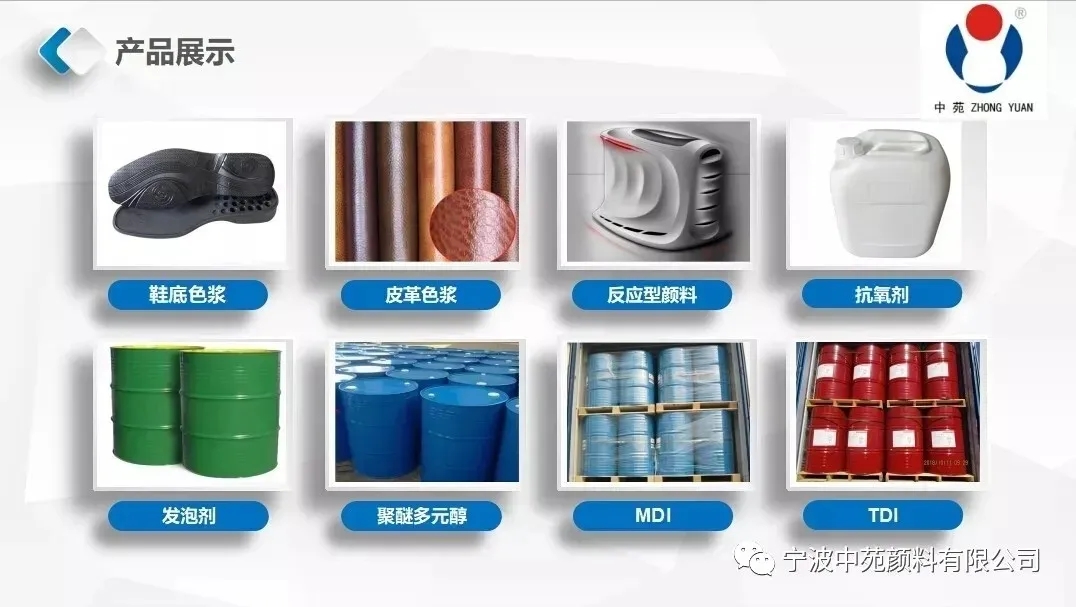
Polyurethane is mainly polymerized with diisocyanate, chain extender, and oligomer polyol as basic raw materials. It has the comprehensive properties of rubber and plastic. It has good mechanical properties, abrasion resistance, oil resistance, tear resistance, chemical corrosion resistance, radiation resistance, good adhesion and other excellent properties, but its use temperature generally does not exceed 80 ℃, and materials above 100 ℃ will soften and deform. The performance is obviously weakened, and the short-term use temperature does not exceed 120 ℃, which severely limits its application in the high temperature field.
Today, the editor reviewed the factors affecting the heat resistance of elastomers from the aspects of oligomer polyols, isocyanates, chain extenders, catalysts, polymerization process conditions, the introduction of intramolecular groups, the addition of fillers, and the composite with nanomaterials.
1. The influence of raw materials on the heat resistance of polyurethane elastomer
Polyurethane elastomer is composed of soft segment (oligomer polyol, mainly divided into polyester type, polyether type and polyolefin type polyol, etc.) and hard segment (diisocyanate and chain extender). The relative molecular mass of oligomer polyols is polydisperse, while polyisocyanates are often a mixture of multiple isomers. The presence of isomers will destroy the regularity of the hard segment and reduce the heat resistance of the elastomer. Strictly controlling the purity of raw materials, reducing the mole fraction of groups with poor thermal stability such as biuret and allophanate, can improve the heat resistance of the elastomer.
1. Oligomer polyol
The thermal decomposition temperature of urethanes formed by the reaction of oligomer polyols of different structures with the same isocyanate is very different. The primary alcohol is the highest and the tertiary alcohol is the lowest. This is because the bond close to the tertiary carbon atom and quaternary carbon atom is the easiest The reason for the break. Since the thermal stability of the ester group is better, and the hydrogen on the carbon atom of the ether group is easily oxidized, the heat resistance of polyester polyurethane is better than that of polyether polyurethane. For polyurethane prepared from polyester, the difference in polyester type has little effect on thermal performance.
For polyether polyurethane, the type of polyether has a certain impact on its heat resistance, such as toluene diisocyanate (TDI), 3,3'-dichloro-4,4'-diphenylmethane diamine (MOCA) ) Polyurethane prepared with polypropylene oxide glycol and polytetrahydrofuran ether glycol (PTMG) respectively. After being aged at 121℃ for 7 days, the tensile strength of the two is obviously different. The tensile strength retention rate of the former at room temperature is 44%, while the latter’s retention rate is 60%. The relative molecular weight or molecular chain length of oligomer polyols has no obvious effect on the characteristic decomposition temperature of thermal degradation of polyurethane. Liu Liangbing studied the degradation mechanism of polyester and polyether polyurethanes, and analyzed the factors affecting their heat resistance. , It is concluded that the heat resistance of polyester polyurethane elastomer is better than that of polyether type.
2. Isocyanate
The hard segment is the main structural factor affecting the heat resistance of polyurethane elastomers. The better the rigidity, regularity and symmetry of the hard segment, the higher the thermal stability of the elastomer. The mass fraction of the hard segment increases, forming more ordered structure and subcrystalline structure of the hard segment, so that the two phases are reversed, the hard segment becomes the continuous phase, and the soft segment is dispersed in the hard segment, thereby improving the stretch of the elastomer at high temperature. Strength and heat resistance. From the point of view of molecular structure, the molecular structure of diphenylmethane diisocyanate (MDl) is similar to that of TDI. Both contain NCO groups and benzene ring structures. However, due to the simplicity, rigidity, regularity and symmetry of the structure, it is an elastomer. The degree of microphase separation is not enough, and the thermal stability of the prepared elastomer is average. In general, the higher the purity of the isocyanate, the fewer the isomers, the higher the regularity and symmetry of the resulting polyurethane elastomer, and the better the heat resistance. The hard segment formed by the isocyanate with regular structure is easy to aggregate, which improves the degree of microphase separation. The polar groups between the hard segments generate hydrogen bonds to form the crystalline region of the hard segment phase, so that the entire structure has a higher melting point.
For example, because 1,5-naphthalene diisocyanate (NDl) has an aromatic naphthalene ring structure, the molecular chain is highly regular, and the synthetic elastomer has excellent properties. Zhen Jianjun et al. synthesized polyurethane elastomers with NDI and TDI and polyethylene adipate propylene glycol (PEPA) respectively. Through thermal weight loss analysis, they found that the thermal decomposition temperature of NDI polyurethane elastomer is higher than that of TDI polyurethane elastomer. In addition, the comparison of high temperature retention of mechanical properties of elastomers at different temperatures shows that the heat resistance of NDI polyurethane elastomer is better than that of TDI polyurethane elastomer.
PPDI-type elastomers prepared from p-phenylene diisocyanate (PPDl), due to the regularity of PPDI structure, heat resistance is several times better than MDI and TDI-type elastomers. The 1,4-cyclohexane diisocyanate (CHDl) is also due to its simple molecular structure, high symmetry and regularity, strong crystallinity, and the prepared elastomer has excellent phase separation. Li Fen, et al. compared the main physical properties of CHDI polyurethane elastomers with polyurethane elastomers made of MDI, PPDI, and methylenedicyclohexyl-4,4',-diisocyanate (HMDl). The results show that CHDI polyurethane elastomer has higher hardness with lower hard segment content, and has better high temperature mechanical properties than MDI, HMDI, and even PPDI elastomers.
In addition, the addition of trimerization catalyst or post-vulcanization process under the premise of excess isocyanate can form stable isocyanate crosslinks in the elastomer, thereby improving the heat resistance of the elastomer.
3. Catalyst
The reaction activity of alicyclic isocyanates is low, and a catalyst must be added to the reaction system to promote the reaction to proceed in the expected direction and speed. The most valuable catalysts are organometallic compounds, and polymer organic carboxylic acids and tertiary amine compounds can also promote the chemical reaction of isocyanates.
Zhang Xiaohua, et al. synthesized transparent polyurethane elasticity with PTMG, isophorone diisocyanate (1PDl), 1,4-butanediol (BDO) and different catalysts, stannous isooctanoate, dibutyltin dilaurate, and promoter K. The effect of the type of catalyst on the mechanical properties, optical transparency, reaction degree and thermal stability of the elastomer was studied. The results show that using the composite catalyst stannous isooctanoate and its promoter K, the promoter K can absorb the CO2 released by the reaction of NCO groups with water and is beneficial to the formation of cross-linking bonds, so the polyurethane elastomer prepared has a better comprehensive Mechanical properties and excellent thermal stability.
4. Crosslinking agent
The excellent properties of polyurethane elastomers are closely related to their physical and chemical cross-linking structures. Physical crosslinking refers to the hydrogen bonding formed between hard segments and between hard and soft segments; chemical crosslinking refers to covalent crosslinking between molecules formed by crosslinking agents.
The generation of chemical cross-linking hinders the mobility of the soft segment. In this way, the spatial freedom of the lattice lattice is reduced, which is not conducive to the crystallization of the soft segment, prevents the hard segments from getting close together, the electrostatic effect is weakened, and the hydrogen bond is difficult to form. Reduce the degree of microphase separation. Zhang Xiaohua, et al. used a one-step method to synthesize a transparent polyurethane elastomer with isophorone diisocyanate, polyoxytetramethylene glycol, 1,4-butanediol and polyoxypropylene triol (N3010) as raw materials. FT-IR, TG and other methods have studied the effects of physical crosslinking and chemical crosslinking on the mechanical properties, optical transparency and thermal stability of polyurethane elastomers. The results show that with the addition of the crosslinking agent triol N3010, the polyurethane elastomer forms crosslinks between the hard segments, and the light transmittance, thermal stability and mechanical properties are significantly improved compared with the polyurethane elastomer without the crosslinking agent.
5. Chain extender
The influence of chain extender on heat resistance is related to its rigidity. Generally speaking, the higher the content of rigid segments, the better the heat resistance of the elastomer. Huang Zhixiong, etc. Use 4,4'-diphenylmethane-5-maleimide and 3,3'-dichloro-4,4'-diphenylmethanediamine (BMI-MOCA) chain extenders to avoid The high activity of MOCA provides favorable conditions for casting large-scale products, and it is also easy to synthesize high-hardness polyurethane elastomers. Due to the introduction of the BMI aromatic ring structure, the relative increase in the rigid segment can significantly improve the thermal stability of the polyurethane elastomer.
In addition, the chain extender hydroquinone bishydroxyethyl ether (HQEE) is a new type of non-toxic chain extender, which can replace MOCA and has many advantages. It is widely used in polyurethane elastomers and can improve polyurethane heat resistance and tear resistance. Cracking strength and storage stability of rubber compound.
2. The effect of polymerization process conditions on the heat resistance of elastomers
The thermal stability of urea and carbamate groups is greater than that of allophanate and biuret, which means that the mole fraction of urea and carbamate groups in the elastomer molecule is increased, and the allophane is reduced. The mole fraction of ester groups and biuret groups can improve the thermal stability of the elastomer, that is, strictly control the process conditions, especially the amount and purity of the reactants, so that the reaction generates as many urea groups and carbamates as possible It is of great significance to improve the heat resistance of elastomers. Chain extension vulcanization with diamine to generate urea groups, control of the reaction of NCO groups and urea groups to generate biuret, and the use of aromatic diisocyanates can effectively improve the heat resistance of polyurethane elastomers. The reaction of polyurethane generally includes one-step method, prepolymerization method and semi-prepolymerization method. The one-step method is relatively simple, but the molecular structure of the product is often irregular and the performance is poor. The prepolymerization method and the semi-prepolymerization method are better.
The German patent reported that a polyurethane elastomer with a softening temperature of 147°C was prepared by a semi-prepolymerization method. In addition, a post-vulcanization condition of more than 4h at a temperature of about 120°C can also improve the heat-resistant deformation performance of the polyurethane elastomer cast rubber.
3. The effect of modification on the heat resistance of polyurethane elastomer
1. The effect of organic silicon modification on the heat resistance of elastomers
Silicone has a unique structure and excellent resistance to high and low temperature and oxidation, excellent electrical insulation and thermal stability, excellent air permeability and biocompatibility, etc. Silicone modified polyurethane elastomer has high Heat resistance, its heat distortion temperature can reach 190℃.
The reason for its good heat resistance is that, on the one hand, the thermal stability of the SiO2 bond is good, and on the other hand, the soft segment mainly composed of siloxane has good flexibility, which is beneficial to microphase separation. Stanciu A and others used polyadipate L-alcohol ester glycol (PEGA), hydroxyl-terminated polydimethylsiloxane (PDMS-OH), MDI and maleic acid diglyceride polyol to prepare cross-linked Polyester-polysiloxane-polyurethane elastomer, performance test shows that PDMS-OH has little effect on the mechanical properties of the final material, but the stability and elasticity at low temperatures are improved, and the thermal stability is better.
Wen Sheng, et al. synthesized a series of siloxane-containing polyurethane elastomers by using polydimethylsiloxane (PDMS) with terminal groups as hydroxyl groups and polytetrahydrofuran ether glycol as a mixed soft segment. Thermogravimetric analysis (TGA) showed , The introduction of PDMS improves the thermal stability of traditional polyurethane elastomers.
2. The influence of the introduction of intramolecular groups on the heat resistance of elastomers
The thermal decomposition temperature of polyurethane elastomer mainly depends on the heat resistance of various groups in the macromolecular structure. If there is a double bond in the soft segment, it will reduce the heat resistance of the elastomer, while the introduction of isocyanurate rings and inorganic elements can improve the heat resistance of the polyurethane elastomer. Introducing a heterocyclic ring with good thermal stability (such as isocyanurate ring, polyimide ring, oxazolidinone ring, etc.) into the main chain of the PU molecule can significantly improve the heat resistance of the polyurethane elastomer.
The trimer of aliphatic or aromatic polyisocyanate contains an isocyanurate ring, which has excellent heat resistance and dimensional stability, and its products can be used for a long time at 150°C. The polyimide produced by the reaction of dicarboxylic anhydride and diisocyanate has the characteristics of insoluble and high temperature resistance. The introduction of polyimide ring into PU can improve the heat resistance and mechanical stability of polyurethane elastomer. The oxazolidinone compound produced by the reaction of epoxy group and isocyanate in the presence of a catalyst has good thermal stability. The thermal decomposition temperature exceeds 300°C, and the glass transition temperature reaches 150°C, which is significantly higher than that of ordinary polyurethane elastomers. .
3. The effect of compounding with nanoparticles and fillers on the heat resistance of elastomers
Nanomaterials are "the most promising materials in the 21st century." Polymer-based nanocomposites mean that the size of the dispersed phase is at least one dimension in the nanoscale range. Due to the unique properties of the nano particles, the mechanical properties of the polyurethane elastomer are significantly improved, and the heat resistance and anti-aging properties of the elastomer can be increased. The composite of nanoparticles and elastomers is a new type of composite material system worthy of research and development.
Gilman JW, et al. showed that the X-ray diffraction results of the polyurethane-montmorillonite nanocomposite showed that the montmorillonite was dispersed in the polyurethane matrix with an average interlayer spacing of not less than 415nm, and the silicate in the montmorillonite played a role in heat insulation. It can effectively improve the heat resistance of composite materials. ZhuY et al. used the excellent comprehensive properties of polyurethane elastomer and inorganic particles-nano-SiO2 to prepare SiO2 polyurethane elastomer nanocomposites by the sol-gel method. The experimental results show that the addition of nano-SiO2 can significantly improve the mechanical properties of the polyurethane elastomer matrix and also improve its heat resistance.
Fillers such as calcium carbonate, carbon black, quartz stone, carbon fiber, glass fiber, nylon, and cured resin particles can also improve the heat-resistant deformation performance of the polyurethane elastomer. Du Hui, et al. studied the influence of different inorganic fillers on the mechanical properties and heat resistance of polyurethane elastomers, and the results showed that the mechanical properties and heat resistance of micron-level inorganic fillers modified polyurethane elastomers are significantly better than those of ordinary polyurethane elastomers. .
Four, formula design and application
There are many ways to improve the heat-resistant deformation performance of polyurethane elastomers. In practical applications, reasonable selections should be made according to product performance indicators and process requirements to determine feasible process routes. Although improving the heat resistance of polyurethane elastomers has always been a very active topic in the field of polyurethane elastomers, and a lot of research has been carried out, there are still fewer polyurethane elastomers with excellent comprehensive properties such as heat resistance and mechanical properties, and the overall level is still low. In the laboratory development stage. Exploiting new modification systems and strengthening the industrialization of results are still the main research topics in the polyurethane field in the near future.
Good heat resistance. If PPDI, NDI, TODI and CHDI are to be made into prepolymers, the NDI activity is too high, which is not realistic at present (it is said that the Prepolymer Research Institute of Berrebayr has successfully synthesized good storage stability NDI prepolymer), the rest is fine. Generally speaking, thermal stability and yellowing are required, CHDI is better, and PPDI, which requires heat resistance and dynamic mechanical properties, is better. When TODI is extended with amines, the performance is very close to that of NDI.


We respect originality. The copyright belongs to the original author. When some articles were pushed, the original author could not be contacted due to various reasons. If copyright issues are involved, please contact us and deal with it immediately
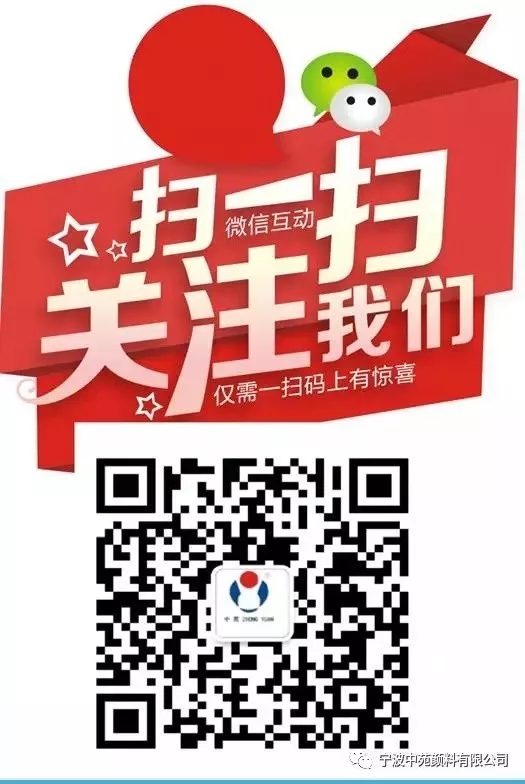
Factory Address: Longzhen Avenue, Longshan Industrial Zone, Cixi, Ningbo
Marketing Center: 1308 Yaojiang Xindu, Hongtang Street, Jiangbei, Ningbo
Telephone: +860574-86501282-0
83096225 83096226
Facsimile: +860574-86501283
Web site:http://zy-pigment.en.alibaba.com/